روش های پوشش نور مقاوم به طور کلی به پوشش اسپین، پوشش غوطه وری و روکش رول تقسیم می شوند که در میان آنها پوشش اسپین بیشترین استفاده را دارد. با پوشش اسپین، فوتوریست روی زیرلایه چکه میشود و میتوان بستر را با سرعت بالا چرخاند تا یک لایه مقاوم به نور ایجاد شود. پس از آن، با گرم کردن آن روی صفحه داغ، می توان یک فیلم جامد به دست آورد. پوشش اسپین برای پوشش از لایه های فوق نازک (حدود 20 نانومتر) تا فیلم های ضخیم حدود 100 میلی متر مناسب است. از ویژگی های آن می توان به یکنواختی خوب، ضخامت فیلم یکنواخت بین ویفرها، عیوب کم و غیره اشاره کرد و می توان فیلمی با عملکرد پوشش دهی بالا به دست آورد.
فرآیند پوشش اسپین
در طول پوشش چرخشی، سرعت چرخش اصلی بستر، ضخامت لایه مقاوم نوری را تعیین می کند. رابطه بین سرعت چرخش و ضخامت فیلم به شرح زیر است:
چرخش = kTn
در فرمول، اسپین سرعت چرخش است. T ضخامت فیلم است. k و n ثابت هستند.
عوامل موثر بر فرآیند پوشش اسپین
اگرچه ضخامت فیلم با سرعت چرخش اصلی تعیین میشود، اما با دمای اتاق، رطوبت، ویسکوزیته مقاوم به نور و نوع مقاومت نوری نیز مرتبط است. مقایسه انواع منحنی های پوشش مقاوم به نور در شکل 1 نشان داده شده است.
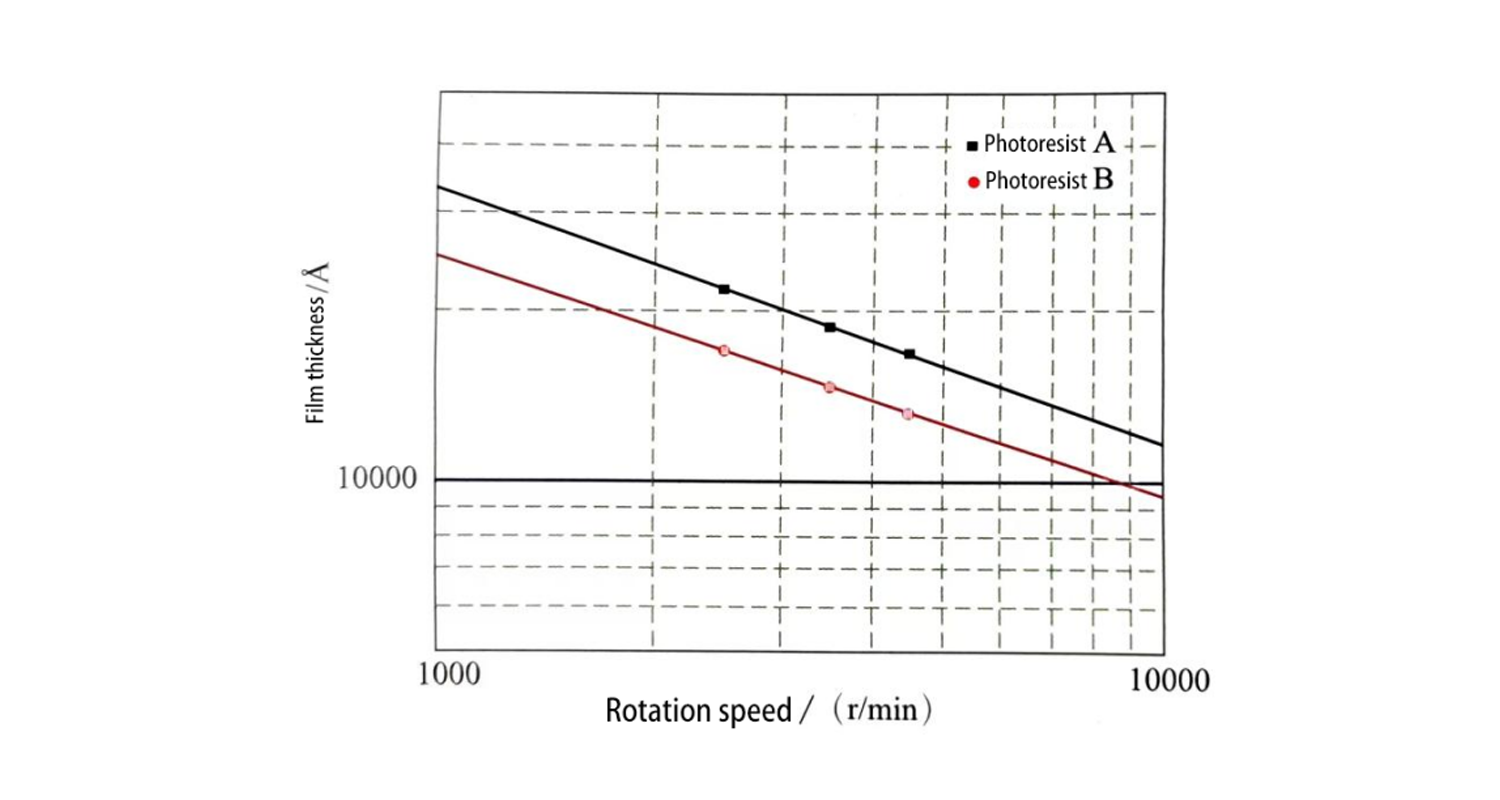
شکل 1: مقایسه انواع منحنی های پوشش مقاوم به نور
تاثیر زمان چرخش اصلی
هر چه زمان چرخش اصلی کوتاهتر باشد، ضخامت فیلم بیشتر می شود. هنگامی که زمان چرخش اصلی افزایش می یابد، لایه نازک تر می شود. وقتی از 20 ثانیه فراتر رفت، ضخامت فیلم تقریباً بدون تغییر باقی می ماند. بنابراین زمان چرخش اصلی معمولا بیش از 20 ثانیه انتخاب می شود. رابطه بین زمان چرخش اصلی و ضخامت فیلم در شکل 2 نشان داده شده است.
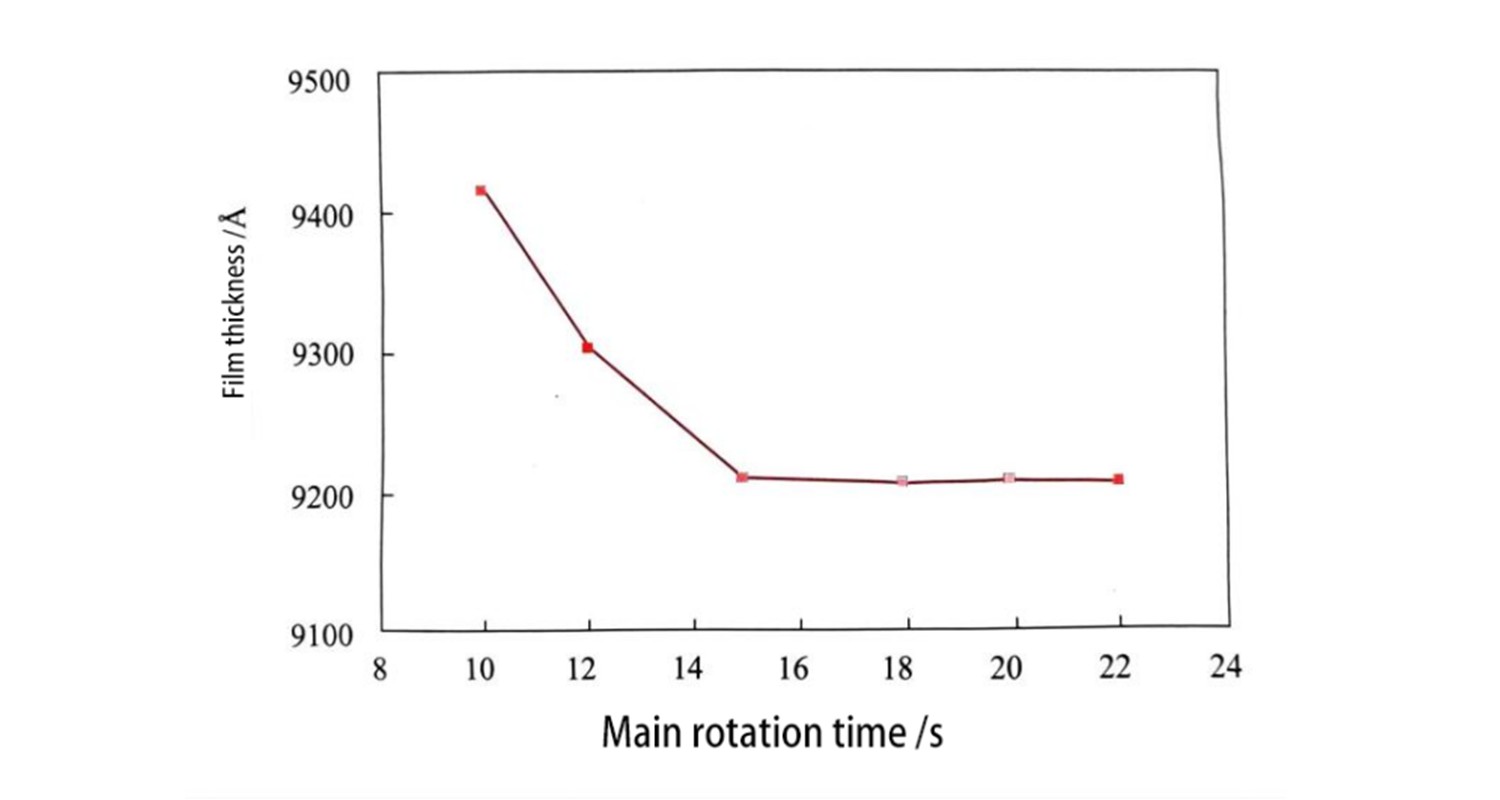
شکل 2: رابطه بین زمان چرخش اصلی و ضخامت فیلم
هنگامی که فترزیست بر روی زیرلایه چکه می شود، حتی اگر سرعت چرخش اصلی بعدی یکسان باشد، سرعت چرخش بستر در حین چکیدن بر ضخامت لایه نهایی تأثیر می گذارد. ضخامت فیلم مقاوم به نور با افزایش سرعت چرخش بستر در طول چکهکنی افزایش مییابد، که به دلیل تأثیر تبخیر حلال هنگام باز شدن نور مقاوم پس از چکیدن است. شکل 3 رابطه بین ضخامت لایه و سرعت چرخش اصلی را در سرعتهای چرخش زیرلایه مختلف در طول چکهکردن مقاومت نوری نشان میدهد. از شکل می توان دریافت که با افزایش سرعت چرخش لایه چکاننده، ضخامت لایه سریعتر تغییر می کند و این تفاوت در ناحیه با سرعت چرخش اصلی کمتر آشکارتر است.
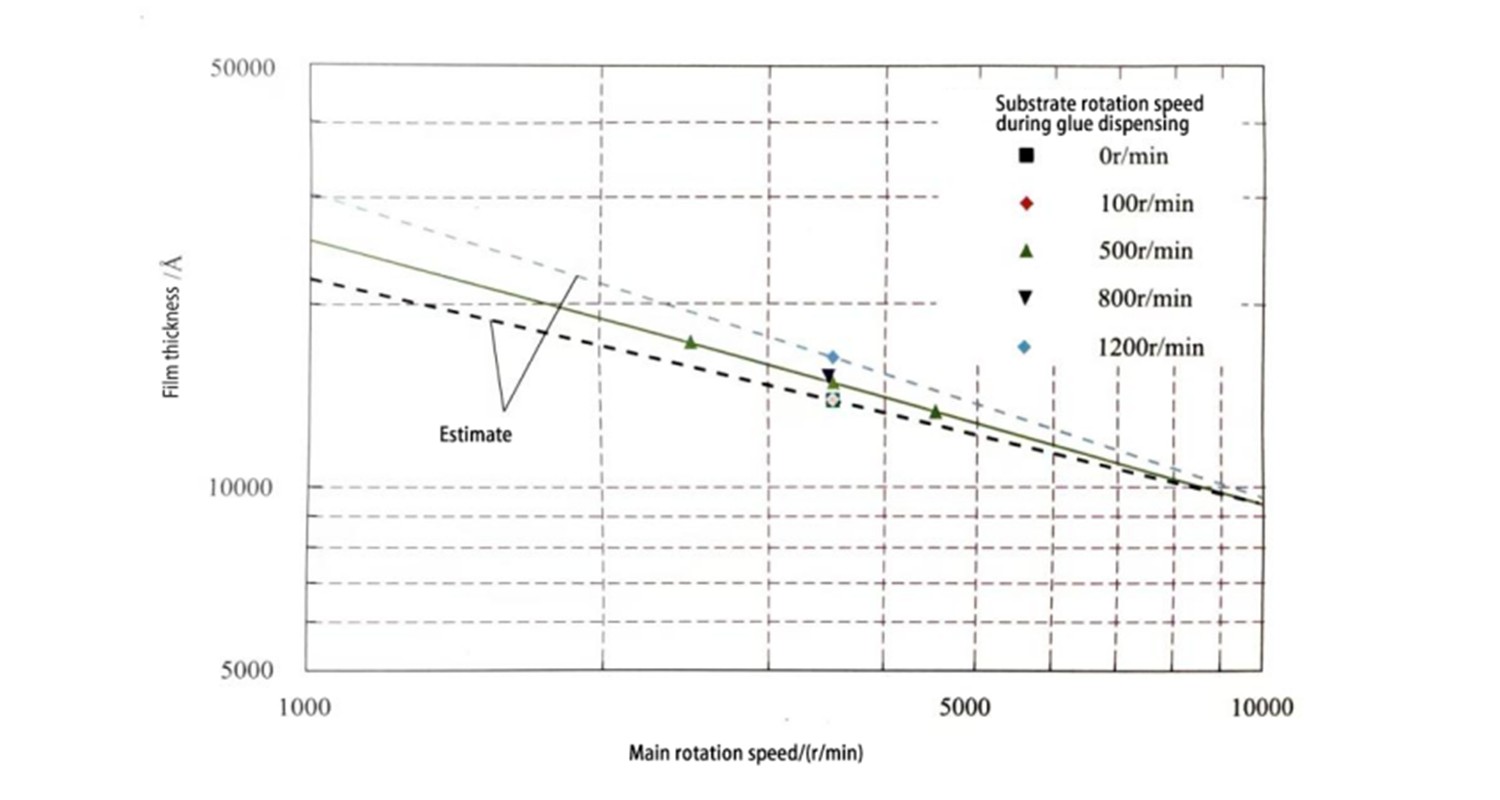
شکل 3: رابطه بین ضخامت لایه و سرعت چرخش اصلی در سرعتهای چرخش زیرلایه مختلف در حین توزیع نور مقاوم
اثر رطوبت در هنگام پوشش
هنگامی که رطوبت کاهش می یابد، ضخامت لایه افزایش می یابد، زیرا کاهش رطوبت باعث تبخیر حلال می شود. با این حال، توزیع ضخامت فیلم به طور قابل توجهی تغییر نمی کند. شکل 4 رابطه بین رطوبت و توزیع ضخامت لایه در طول پوشش را نشان می دهد.
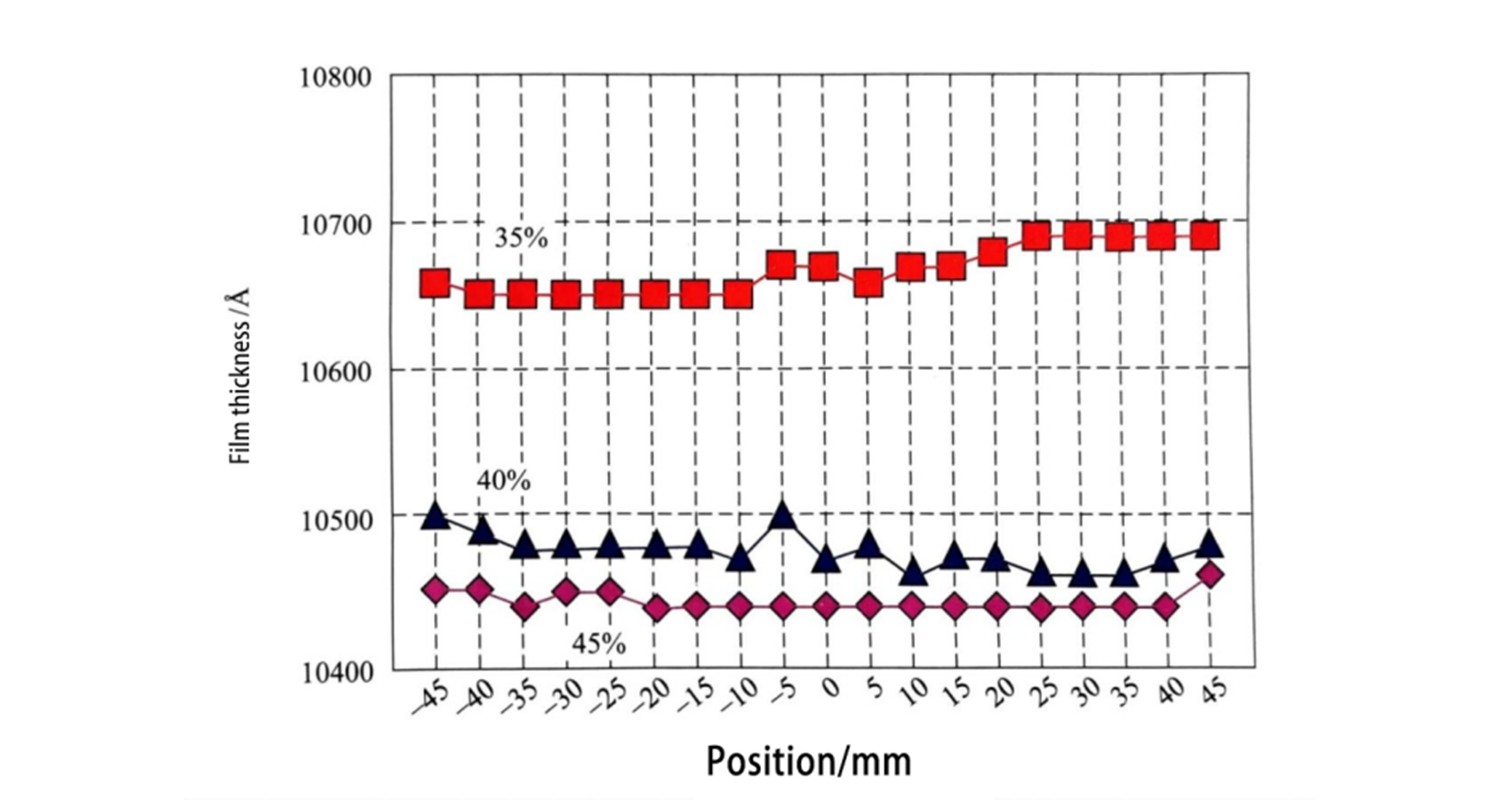
شکل 4: رابطه بین رطوبت و توزیع ضخامت لایه در طول پوشش
تاثیر دما در طول پوشش
هنگامی که دمای داخل خانه افزایش می یابد، ضخامت فیلم افزایش می یابد. از شکل 5 می توان دید که توزیع ضخامت لایه نور مقاوم از محدب به مقعر تغییر می کند. منحنی شکل نیز نشان می دهد که بیشترین یکنواختی زمانی به دست می آید که دمای داخل ساختمان 26 درجه سانتی گراد و دمای مقاومت نوری 21 درجه سانتی گراد باشد.
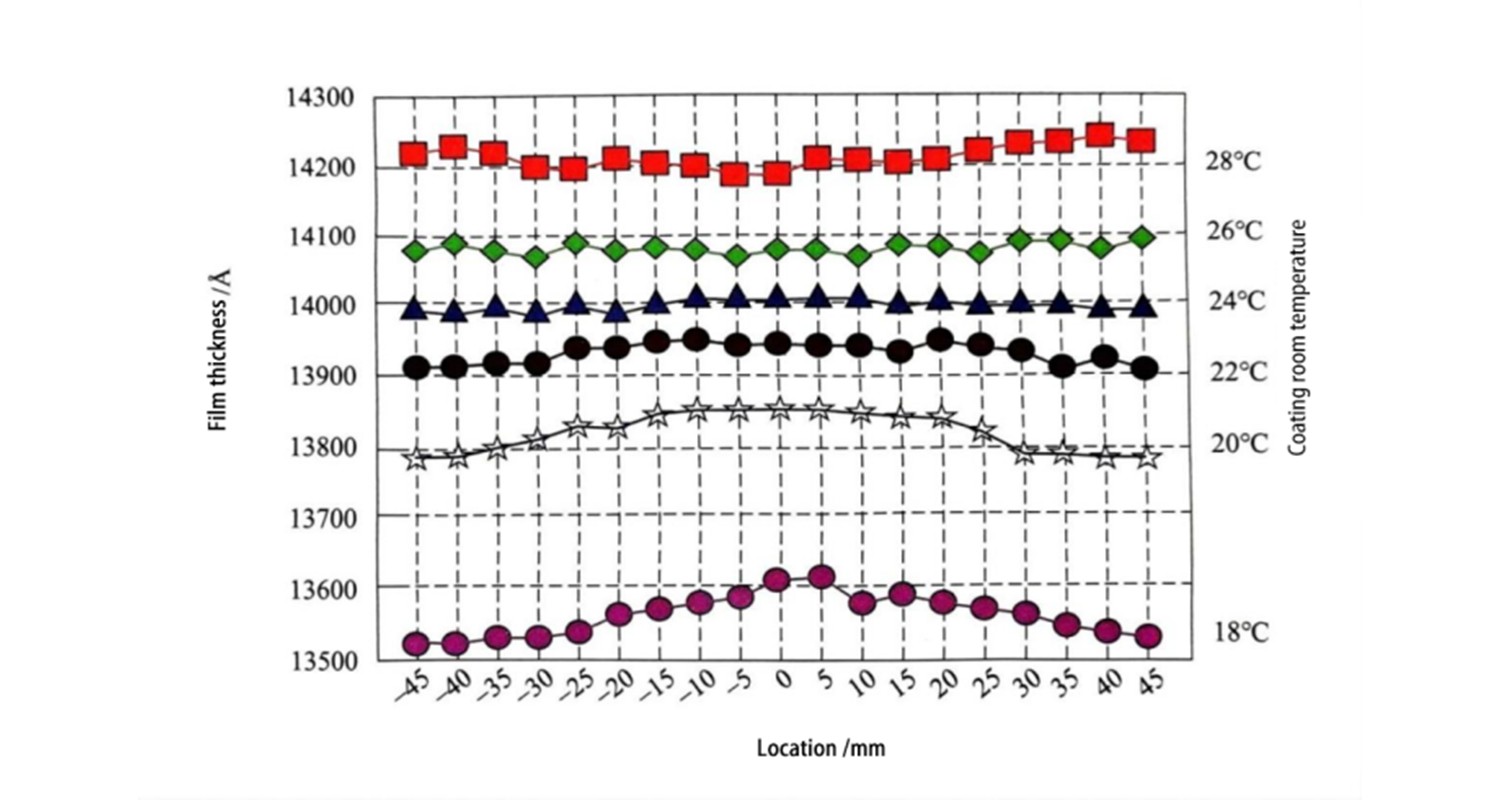
شکل 5: رابطه بین دما و توزیع ضخامت لایه در طول پوشش
اثر سرعت اگزوز در طول پوشش
شکل 6 رابطه بین سرعت اگزوز و توزیع ضخامت فیلم را نشان می دهد. در غیاب اگزوز، نشان می دهد که مرکز ویفر تمایل به ضخیم شدن دارد. افزایش سرعت اگزوز باعث بهبود یکنواختی می شود، اما اگر بیش از حد افزایش یابد، یکنواختی کاهش می یابد. مشاهده می شود که یک مقدار بهینه برای سرعت اگزوز وجود دارد.
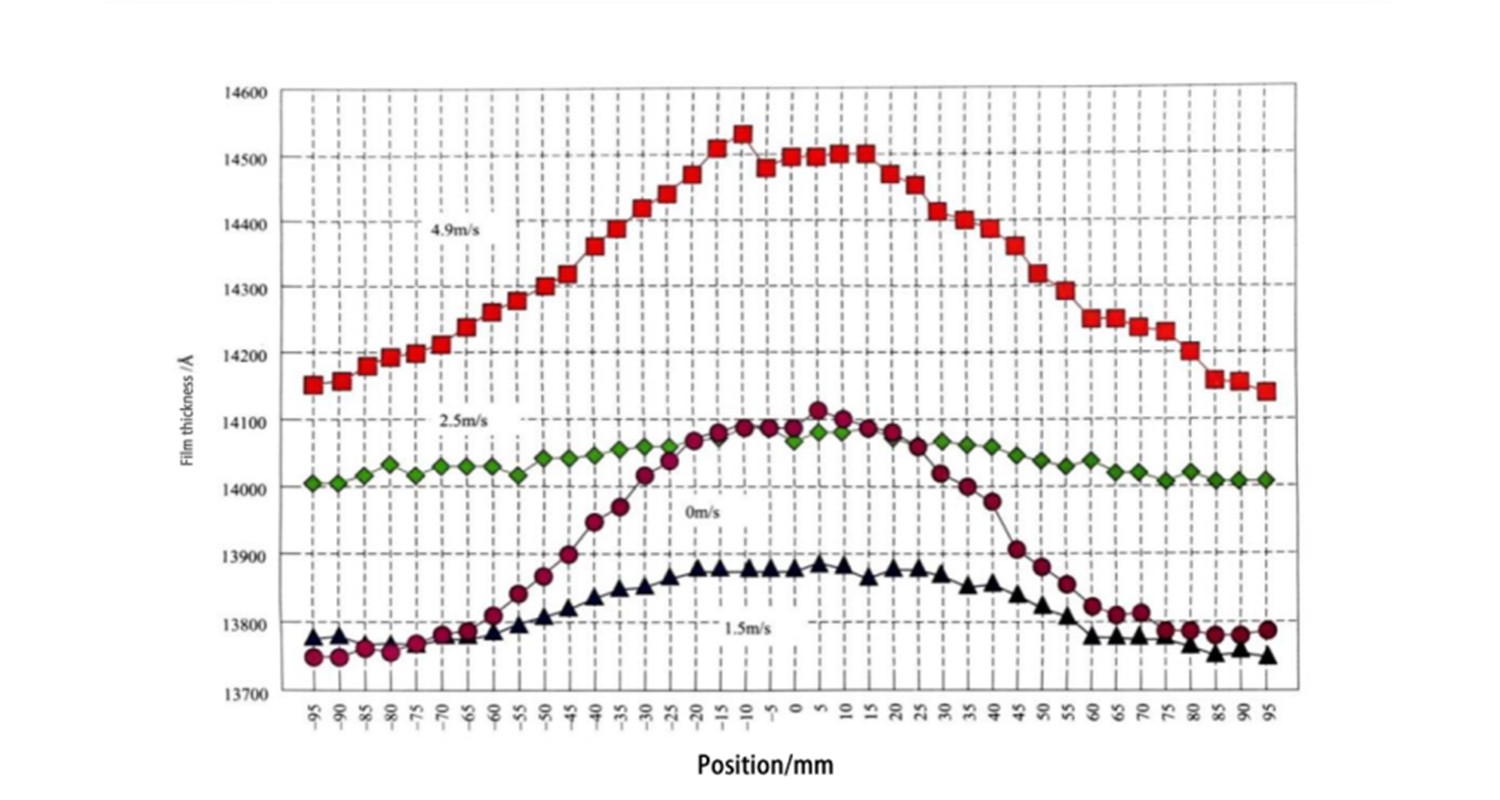
شکل 6: رابطه بین سرعت اگزوز و توزیع ضخامت فیلم
درمان HMDS
به منظور پوشش دهی بیشتر مقاوم به نور، ویفر باید با هگزامتیل دیسیلازان (HMDS) درمان شود. به خصوص هنگامی که رطوبت به سطح فیلم اکسید سی متصل می شود، سیلانول تشکیل می شود که چسبندگی نور مقاوم را کاهش می دهد. به منظور از بین بردن رطوبت و تجزیه سیلانول، ویفر معمولاً در دمای 100-120 درجه سانتیگراد گرم می شود و HMDS مه برای ایجاد یک واکنش شیمیایی وارد می شود. مکانیسم واکنش در شکل 7 نشان داده شده است. از طریق عملیات HMDS، سطح آب دوست با زاویه تماس کوچک به یک سطح آبگریز با زاویه تماس بزرگ تبدیل می شود. حرارت دادن ویفر می تواند چسبندگی مقاوم به نور بیشتری را به دست آورد.
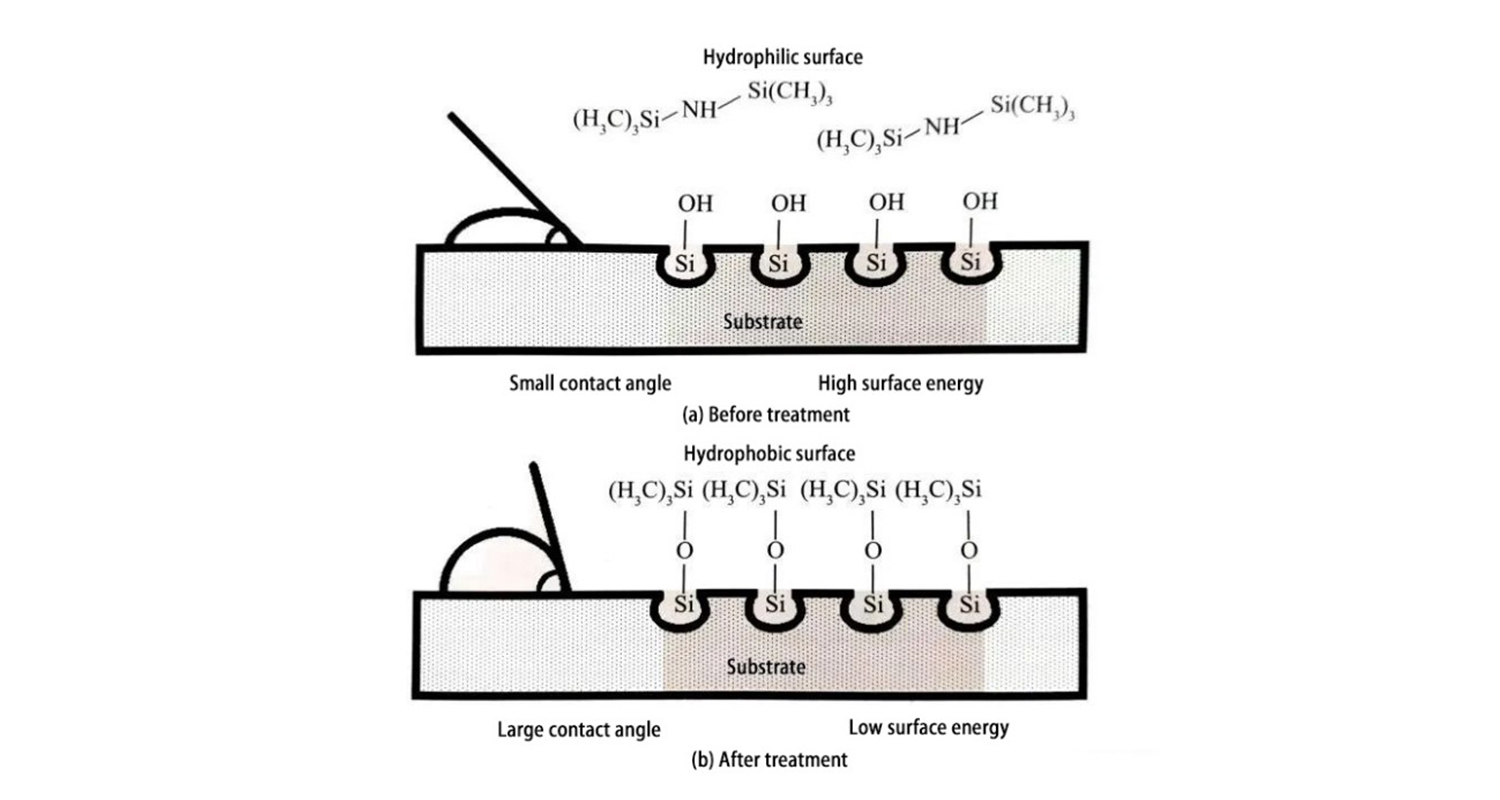
شکل 7: مکانیسم واکنش HMDS
اثر درمان HMDS را می توان با اندازه گیری زاویه تماس مشاهده کرد. شکل 8 رابطه بین زمان درمان HMDS و زاویه تماس (دمای تیمار 110 درجه سانتی گراد) را نشان می دهد. بستر Si است، زمان درمان HMDS بیشتر از 1 دقیقه، زاویه تماس بیشتر از 80 درجه است و اثر درمان پایدار است. شکل 9 رابطه بین دمای عملیات HMDS و زاویه تماس (زمان درمان 60 ثانیه) را نشان می دهد. هنگامی که دما از 120 درجه بالاتر می رود، زاویه تماس کاهش می یابد، که نشان می دهد HMDS در اثر گرما تجزیه می شود. بنابراین، درمان HMDS معمولا در دمای 100-110 درجه سانتیگراد انجام می شود.
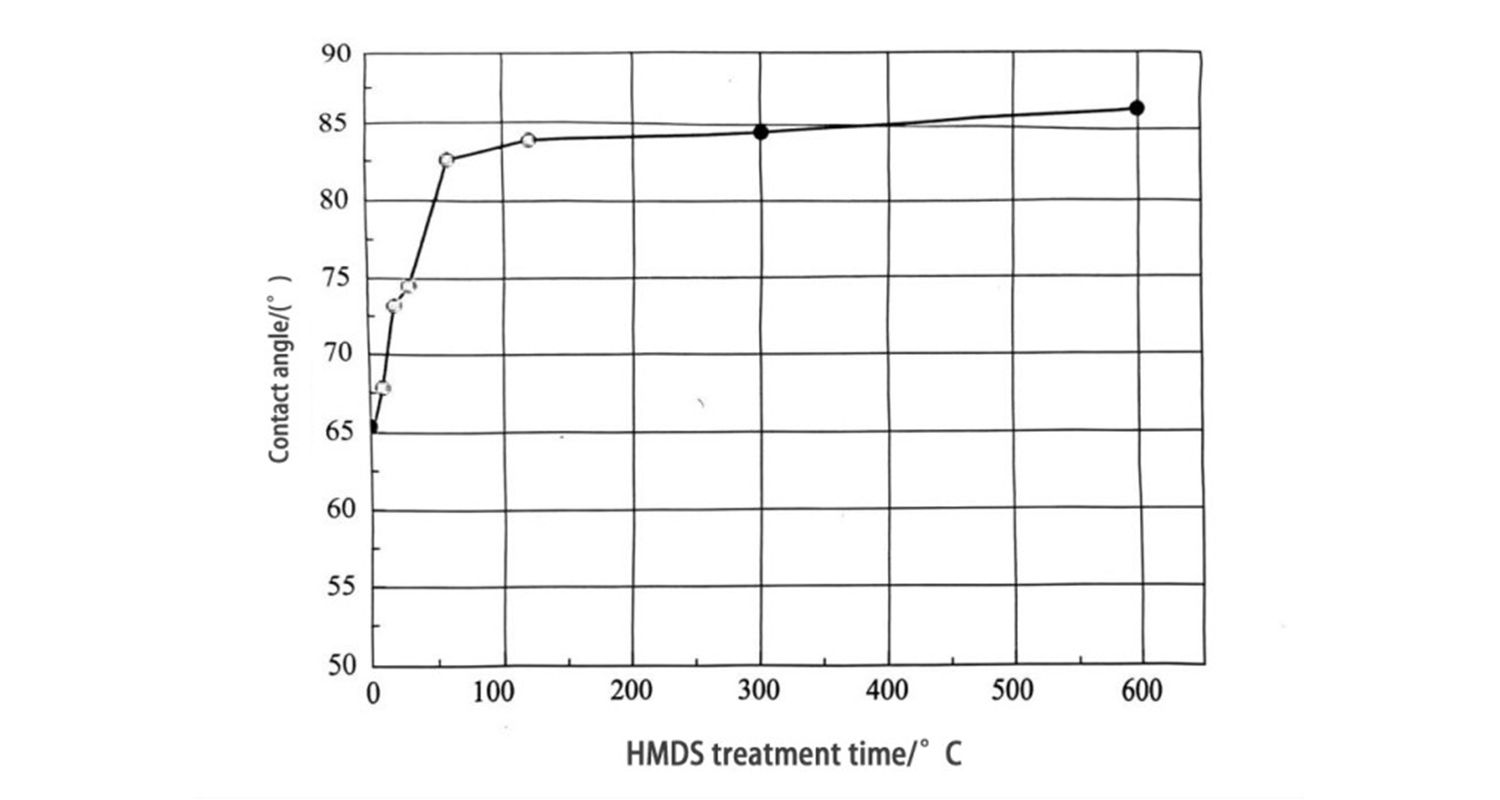
شکل 8: رابطه بین زمان درمان HMDS
و زاویه تماس (دمای درمان 110 درجه سانتیگراد)
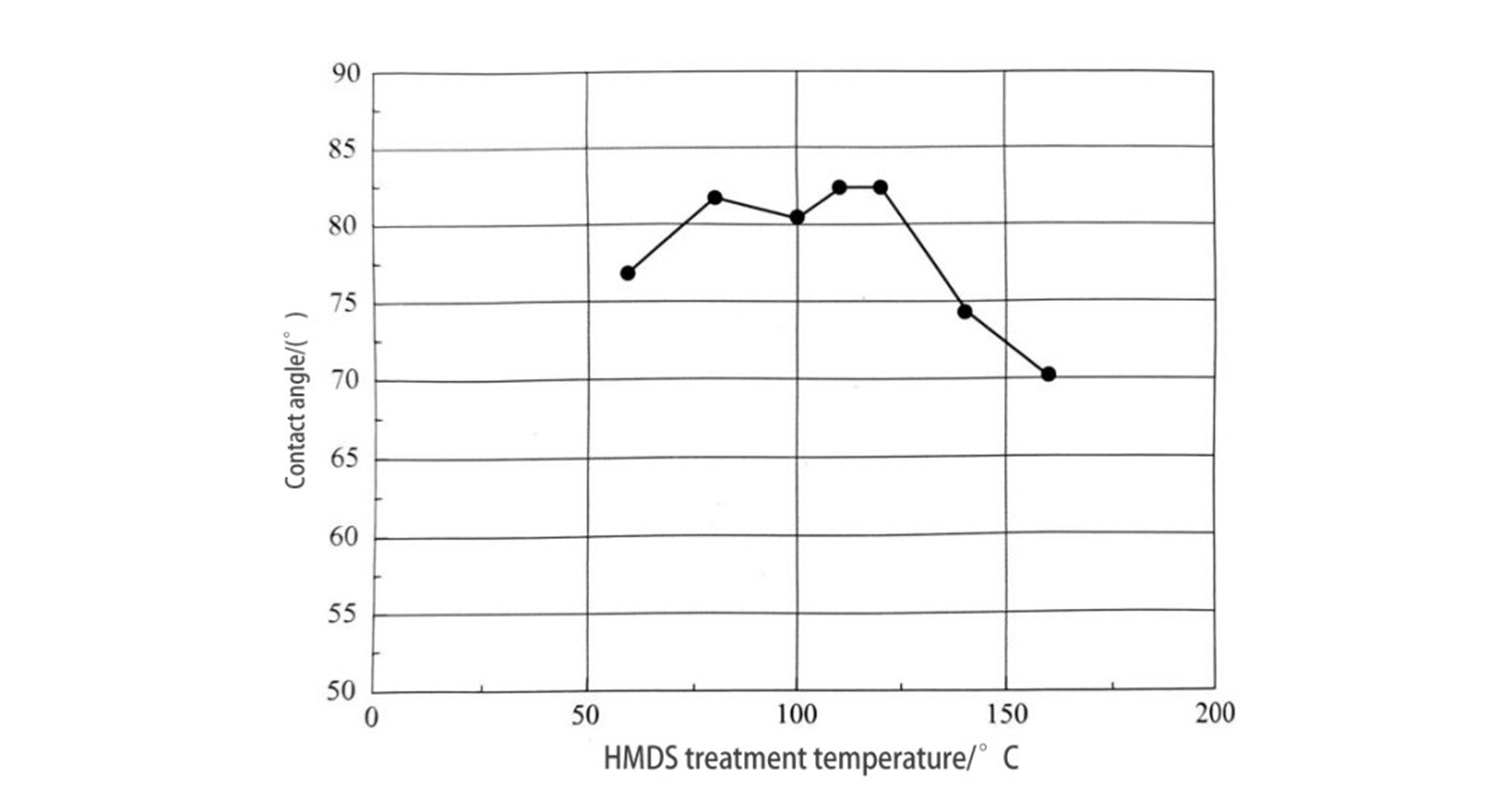
شکل 9: رابطه بین دمای عملیات HMDS و زاویه تماس (زمان درمان 60 ثانیه)
عملیات HMDS بر روی یک بستر سیلیکونی با یک لایه اکسید انجام می شود تا یک الگوی مقاوم به نور ایجاد شود. سپس فیلم اکسید با اسید هیدروفلوئوریک و بافر اضافه میشود و مشخص میشود که پس از عملیات HMDS، میتوان از افتادن الگوی مقاوم نوری جلوگیری کرد. شکل 10 اثر درمان HMDS را نشان می دهد (اندازه الگو 1um است).
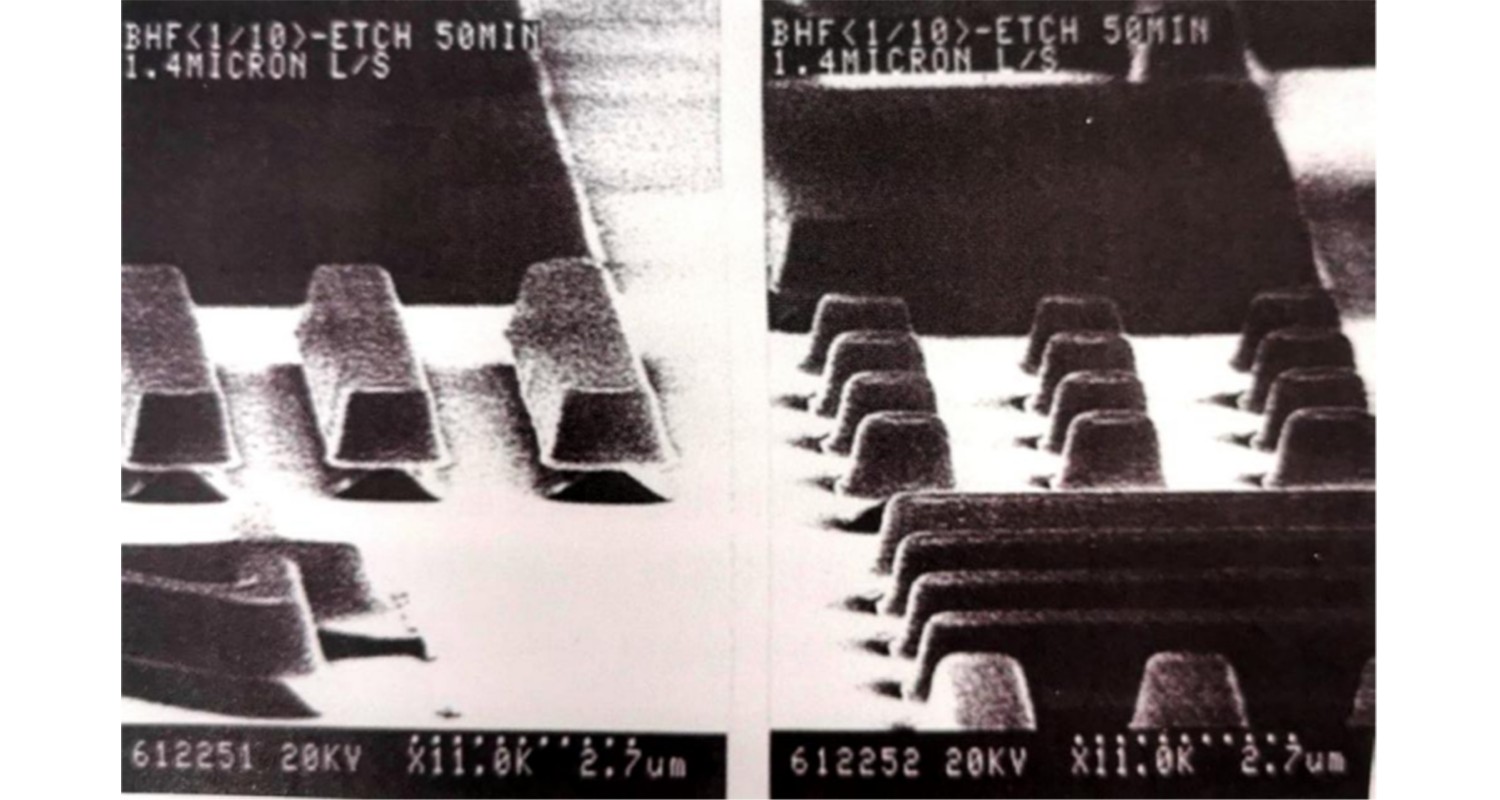
شکل 10: اثر درمان HMDS (اندازه الگو 1um است)
پیش پخت
در همان سرعت چرخش، هرچه دمای پیش پخت بیشتر شود، ضخامت لایه کمتر می شود، که نشان می دهد هر چه دمای پیش پخت بالاتر باشد، حلال بیشتر تبخیر می شود و در نتیجه ضخامت لایه نازک تری ایجاد می شود. شکل 11 رابطه بین دمای قبل از پخت و پارامتر Dill's A را نشان می دهد. پارامتر A غلظت عامل حساس به نور را نشان می دهد. همانطور که از شکل مشخص است، زمانی که دمای قبل از پخت به بالای 140 درجه سانتی گراد می رسد، پارامتر A کاهش می یابد که نشان می دهد عامل حساس به نور در دمای بالاتر از این تجزیه می شود. شکل 12 انتقال طیفی را در دماهای مختلف قبل از پخت نشان می دهد. در دمای 160 درجه سانتیگراد و 180 درجه سانتیگراد، افزایش گذردهی را می توان در محدوده طول موج 300-500 نانومتر مشاهده کرد. این تایید می کند که عامل حساس به نور در دمای بالا پخته و تجزیه می شود. دمای قبل از پخت مقدار بهینه ای دارد که با ویژگی های نور و حساسیت تعیین می شود.
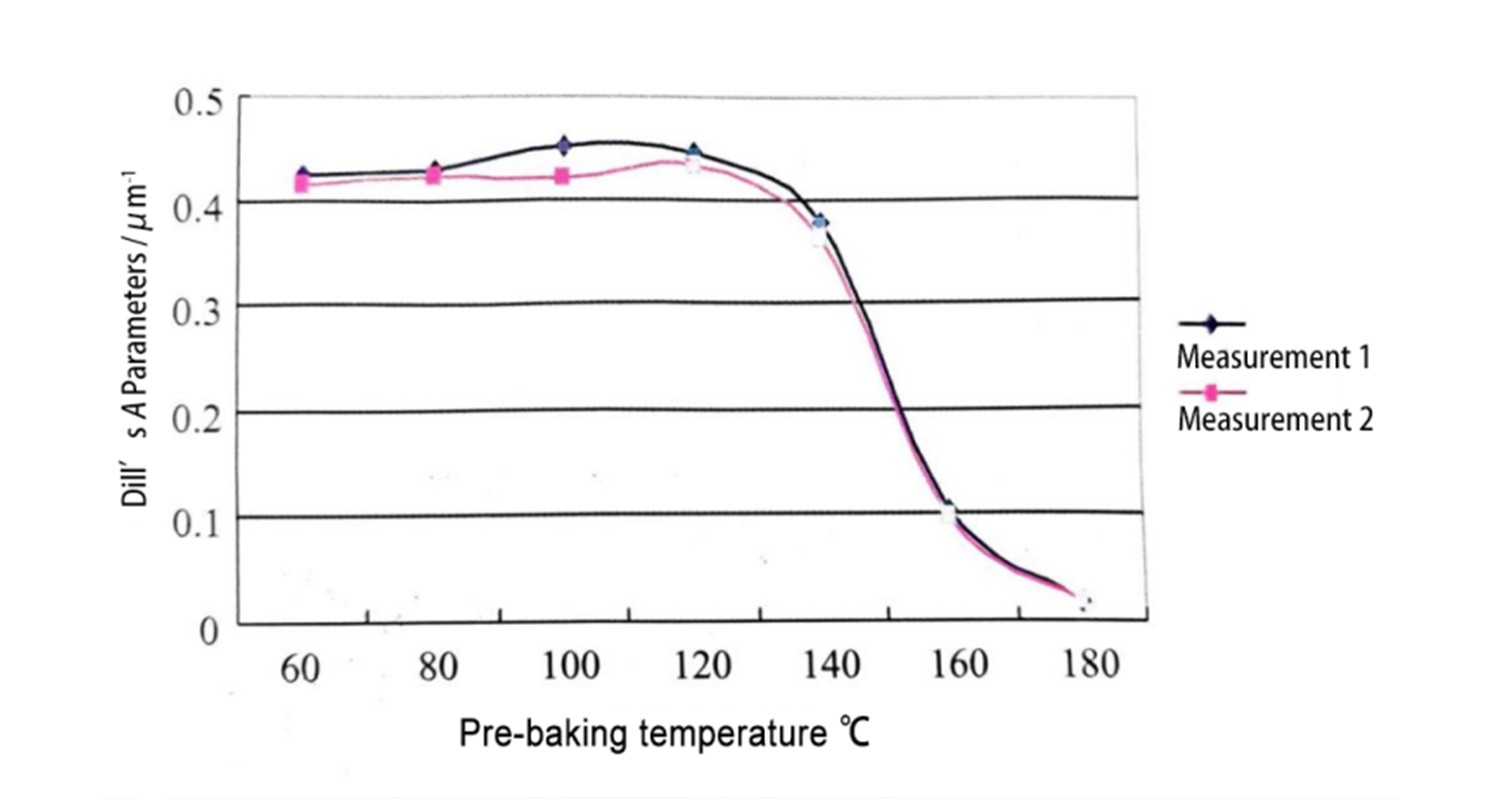
شکل 11: رابطه بین دمای قبل از پخت و پارامتر Dill's A
(مقدار اندازه گیری شده OFPR-800/2)
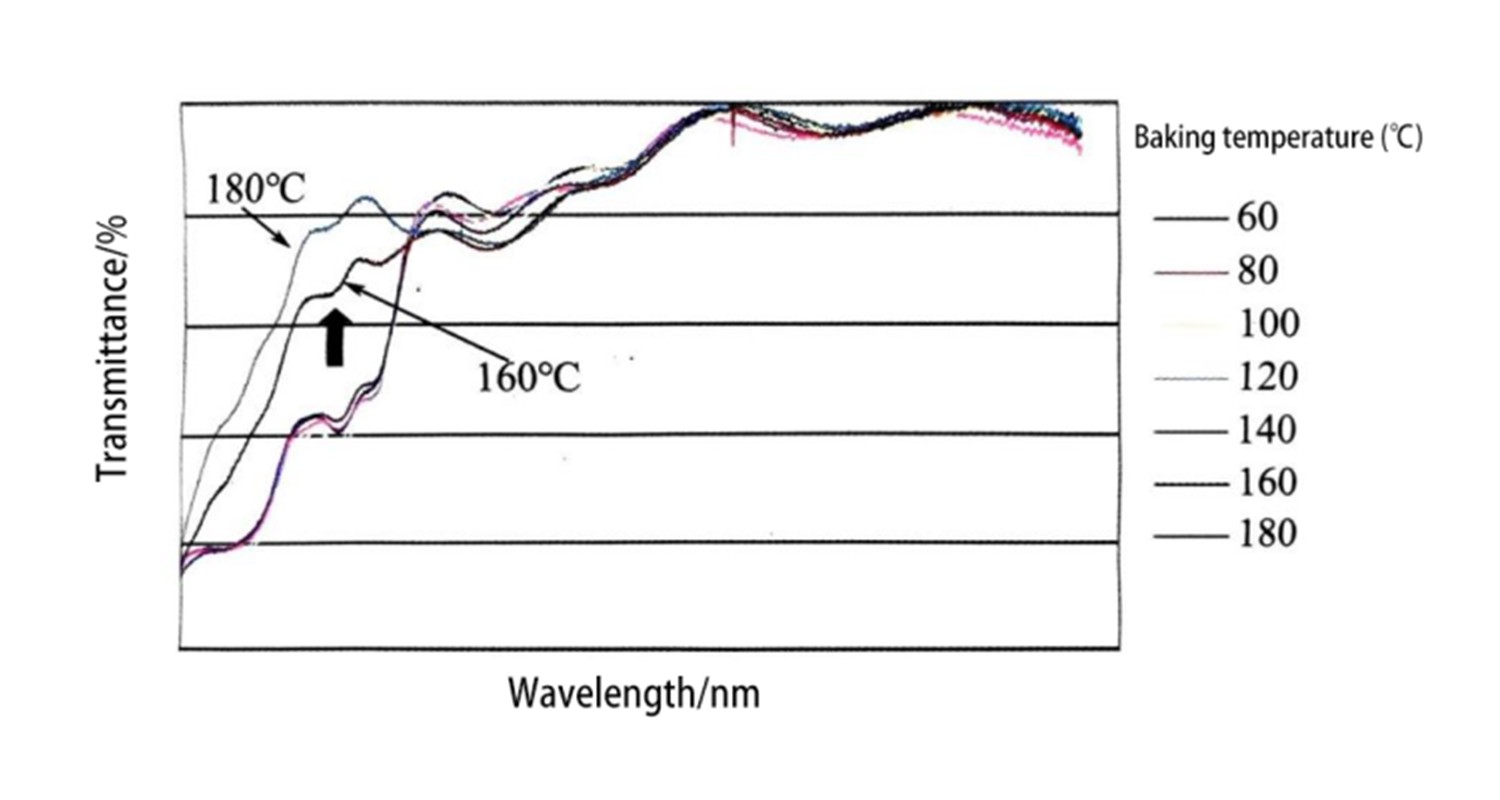
شکل 12: انتقال طیفی در دماهای مختلف قبل از پخت
(OFPR-800، ضخامت فیلم 1 میلی متر)
به طور خلاصه، روش پوشش اسپین دارای مزایای منحصر به فردی مانند کنترل دقیق ضخامت لایه، عملکرد هزینه بالا، شرایط فرآیند ملایم و عملکرد ساده است، بنابراین اثرات قابل توجهی در کاهش آلودگی، صرفه جویی در انرژی و بهبود عملکرد هزینه دارد. در سال های اخیر روکش اسپین توجه روزافزونی را به خود جلب کرده و کاربرد آن به تدریج در زمینه های مختلف گسترش یافته است.
زمان ارسال: نوامبر-27-2024